異色、異材質成形品
一般的な単色成形では一部異なる材質の製品や、一部色分けした製品の実現が難しい。そこで専用機械、成形方式を導入。
ロータリー式2色成型機を導入する事で、1サイクルで異色の樹脂もしくは異なる材質を交互に成形し2種の樹脂で1つの成形品を作ることが可能となりました。工数・コスト削減の他、異色・異材質の組み合わせによる製品への多様な機能の追加など、製品の付加価値率もアップされます。
その他にも成形方式としてインサート成形を採用する事により、金属と樹脂が一体となった成形品も作ることが可能となりました。それに加え金属部品の搬送ロボットを導入する事で効率の良い全自動成形が実現し、作業員のコスト削減にも繋がりました。
いずれも金型製作に複雑な技術が必要となりますが、自社での多岐にわたる金型加工技術を用い自社製作する事でイニシャルコストも削減されました。
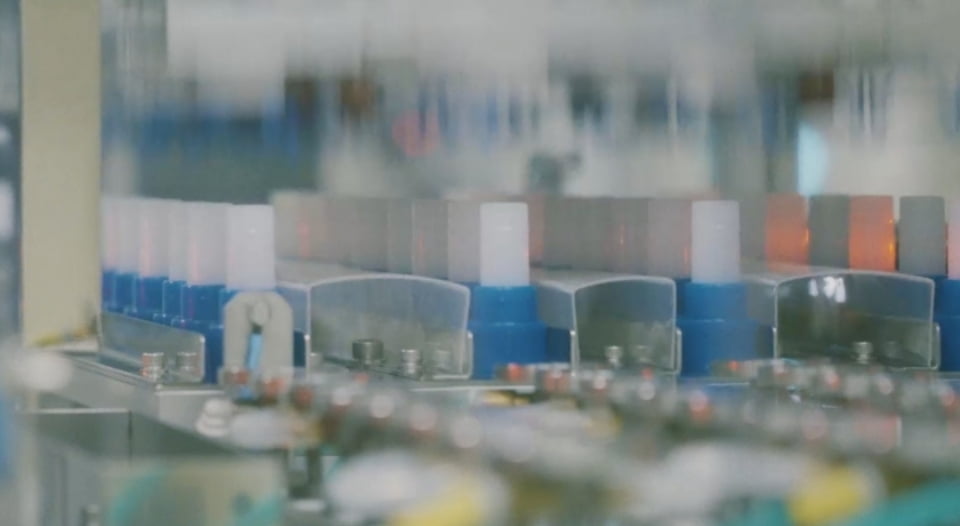
パット印刷、ホットスタンプ加工
一部製造ライン間(成形~製品収納間)に、パット印刷機やホットスタンプ機を設置する事により、一連の流れで成形品に印刷が可能となりました。
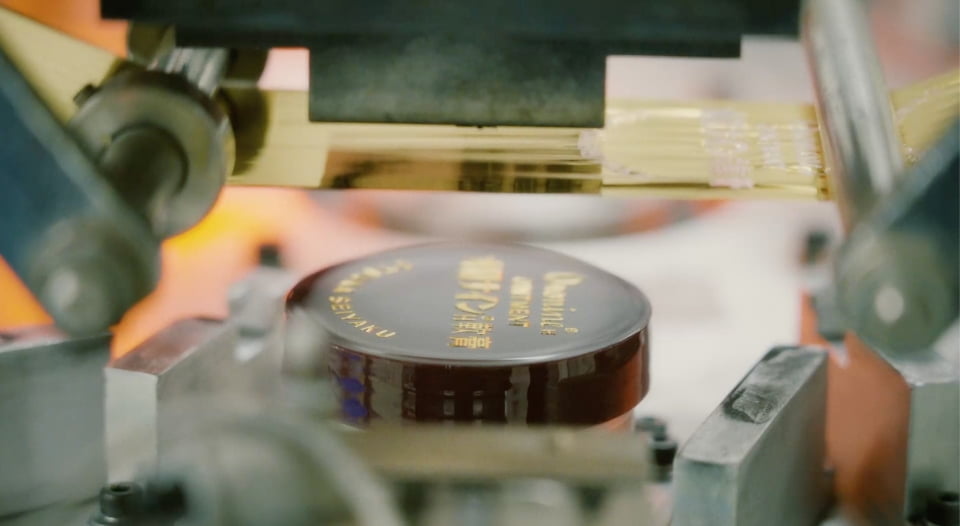
金型に多孔体金属を使用
射出成形には金型に樹脂が充填される際のガス発生問題がつきものです。弊社ではプラスチック素材の他、エラストマー素材も扱っており、このエラストマー素材でガス発生問題に悩まされてきました。これが要因となり、ウエルド・ショートショット(充填不良)・ガスやけ・気泡といった成形不良が発生し易くなります。一般的な対策として、ガスベント(エアーベント)を工夫する事で十分にガス抜きを行うことが挙げられますが、対処しきれない場合もあります。
このような時に解決策として、エラストマー製品の金型に一部多孔体金属を採用しました。
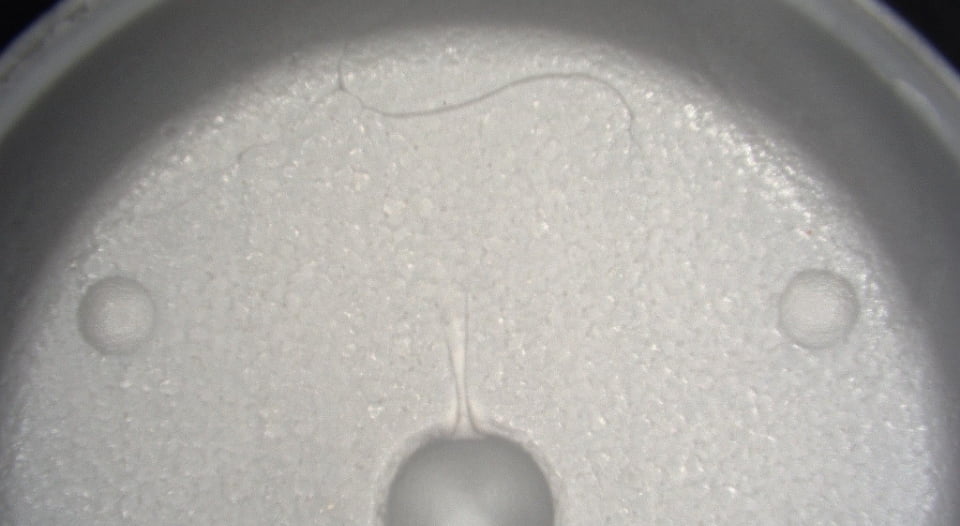
▲多孔体金属 採用前
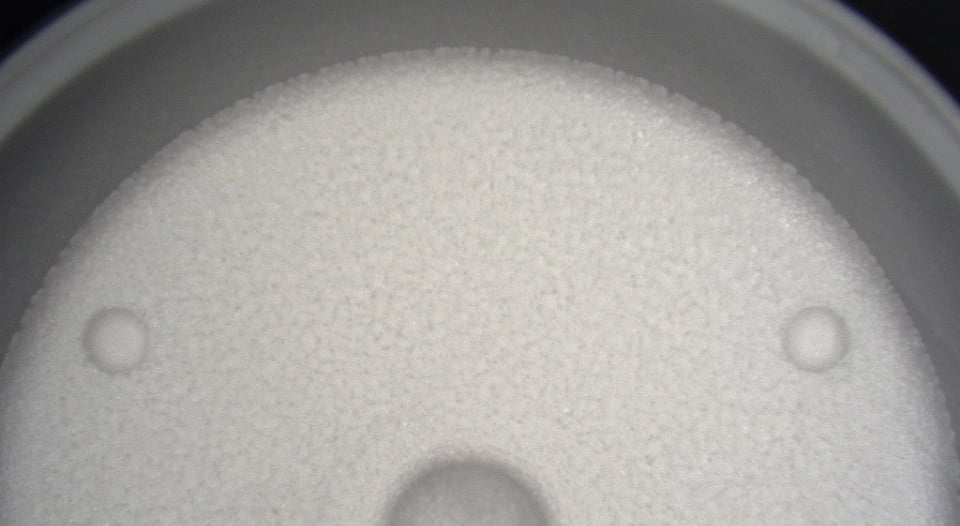
▲多孔体金属 採用後
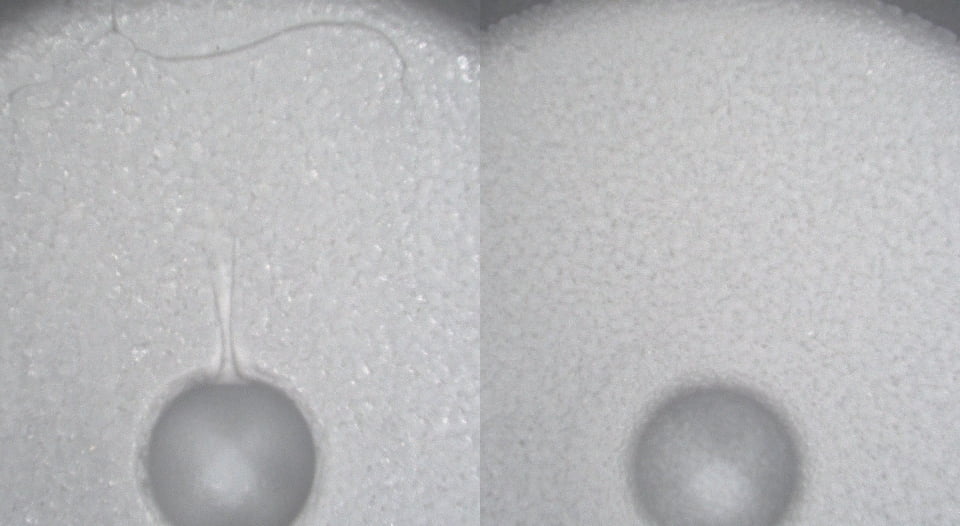
▲比較
このように、多孔体金属を使用する事によりガスベントでのガス抜きに加え、製品面からもガス抜きを行うことでウエルドやガス焼けを改善する事に成功しました。こういった解決策を導き出すことも泉製作所の社内一貫システムが強みとなっております。